Blog
GRIND TRAK TM - Solution for Optimising your Process Needs
10 Aug 2014
In-process diagnostics is very useful for optimization of the grinding system as it reveals to us the nature of the various microscopic interactions taking place in the grinding zone. By understanding how each of the inputs affect the grinding process and how the process itself affects the output, it enables us to identify opportunities in which to improve the grinding system as a whole, rather than just optimizing it in pockets.
Problem: Face Burn marks on component - Counter Shaft
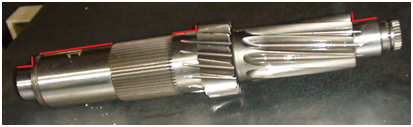
Grind Trak in use
Figure 1: Signature of the initial grinding cycle
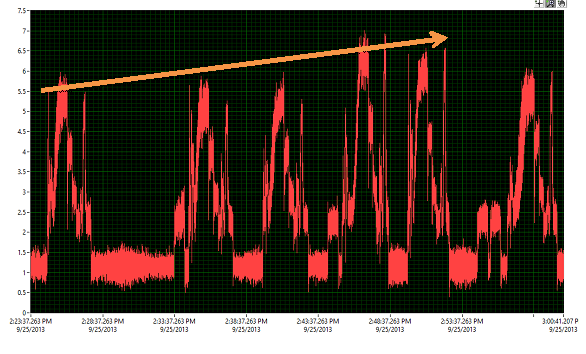
Figure 2: Signature of the grinding cycle after Optimisation
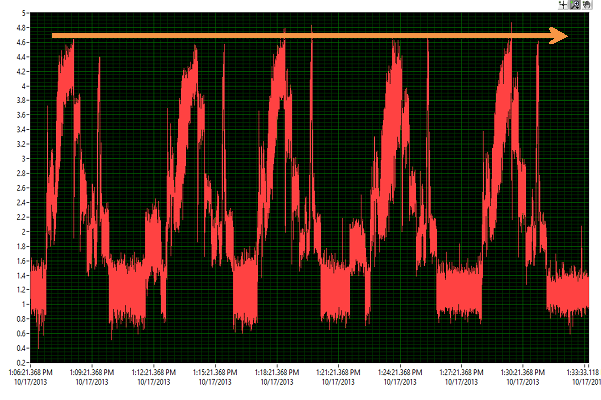
Process Dynamics
In-process signal acquisition and analysis of the grinding process enabled us to identify the factors that could be modified to avoid grinding burn marks on component face.
Grind-Trakwas used to capture the power signals during the grinding process. It was observed that thepeak power and threshold power being consumed by the wheel head motor was increasing after grinding some components, which was an indication that wheel property is changing. This might be due to wheel glazing or over loading. It was observed that the wheel was getting glazed after grinding few components.
To avoid this problem an open structured grinding wheel was used which was having more voids for easy chips flowing.This resulted in lesser peak& threshold power even after grinding ānā number of components. After optimisation the signals showed consistency in the wheel behaviour compared to the initial grinding signal.
System Output
1. Reduced the number of setups from 4 to 2 by using specially dressed profile grinding wheel. Hence increased productivity.
2. Reduction in material handling time.
3. Lesser cycle time by optimized process parameters.
Comments
Yuvraj
Excellent Article....